Intricate moldmaking (high strength, addition-cure products)
KE-1300T, KE-1600 and KE1603 (A-B)
These addition-cure products all have the superior tensile strength, high tear strength and elongation characteristics. These products are used to make vacuum cast prototypes which require a high level of dimensional accuracy for intricate patterns and details. Since they do not release any by-products, they have a linear shrinkage of 0.1% or less during curing. KE-1300T cures with the addition of 10% of the CAT-1300 curing agent, KE-1600 with the addition of 10% of the CAT-1600 curing agent, while KE-1603 (A-B) cures with a 1:1 mixture of A and B. These products have a higher viscosity than general moldmaking products and air bubbles created during the mixing in of the curing agent will not completely dissipate on their own. Thus a vacuum chamber for de-air should be used prior to pouring the mixture into the mold. Addition-cure products differ from condensation-cure products in that the curing time can be accelerated by heating. These addition-cure products are highly durable when used with urethane, polyester and epoxy resins. Since KE1300T is highly translucent and KE-1603 (A-B) is transparent, one can make split molds with the master still in sight. It should be noted that curing may be inhibited if an addition-cure RTV silicone rubber comes into contact with oil clay, double-sided adhesive tape, synthetic rubber or condensation-cure RTV silicone rubber (see page 15). |
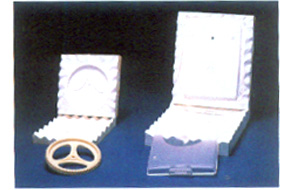
A precision model mold and split mold made using the vacuum casting method |